In today’s fast-paced work environment, achieving optimal organization and efficiency is paramount to success. The 5S Methodology stands as a beacon of workplace excellence—a systematic approach to organization and cleanliness that fosters efficiency, safety, and productivity. Join us as we uncover the essence of the 5S Methodology, explore industry best practices, and discover how to implement this transformative approach in your workplace.
Thank you for reading this post, don't forget to subscribe!Unveiling the 5S Methodology: The Five Pillars of Workplace Excellence
The 5S Methodology is more than just a set of principles; it’s a philosophy—a commitment to creating a workplace environment that is organized, efficient, and conducive to high performance. Originating from Japan, the 5S Methodology encompasses five key pillars: Sort, Set in Order, Shine, Standardize, and Sustain.
Key Components of the 5S Methodology
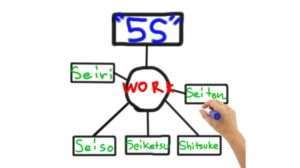
-
Sort (Seiri)
The first step in the 5S Methodology is to sort through items in the workplace, distinguishing between necessary items and unnecessary clutter. By removing unnecessary items, organizations can create a clean and clutter-free work environment that enhances efficiency and productivity.
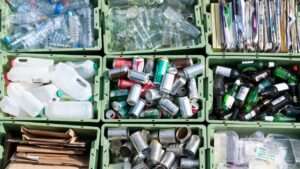
-
Set in Order (Seiton)
Once items have been sorted, the next step is to organize and arrange them systematically. This involves assigning specific locations for tools, equipment, and materials, ensuring that everything has a designated place and is easily accessible when needed.
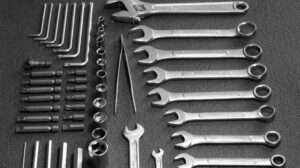
-
Shine (Seiso)
The shine phase involves cleaning and maintaining the workplace to ensure a safe and hygienic environment for employees. Regular cleaning not only improves aesthetics but also reduces the risk of accidents and enhances employee morale and satisfaction.
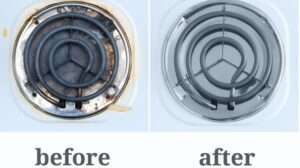
-
Standardize (Seiketsu)
Standardization is key to sustaining the gains achieved through the first three steps of the 5S Methodology. Establishing standardized procedures and protocols for workplace organization and cleanliness ensures consistency and reliability in operations.
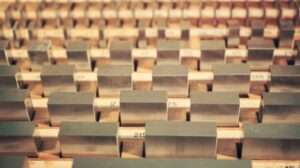
-
Sustain (Shitsuke)
The final step in the 5S Methodology is to sustain the improvements made by continuously reinforcing the 5S principles and practices. This involves ongoing training, communication, and accountability to ensure that the 5S culture is ingrained in the organizational culture.
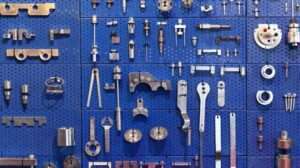
Implementing the 5S Methodology: Practical Strategies for Success
-
Engage Employees
Involve employees at all levels of the organization in the 5S implementation process. Encourage participation, gather feedback, and empower employees to take ownership of their workspace and contribute to continuous improvement efforts.
-
Provide Training and Resources
Offer training and resources to help employees understand the 5S principles and practices and how they can be applied in their daily work. Provide access to tools, supplies, and support to facilitate the sorting, organizing, and cleaning process.
-
Establish Accountability
Hold employees accountable for maintaining the 5S standards and practices in their work areas. Establish clear expectations, conduct regular audits, and recognize and reward employees who demonstrate commitment to the 5S principles.
Real-World Impact of the 5S Methodology: A Case Study
Let’s examine the success story of XYZ Manufacturing, a company that implemented the 5S Methodology to improve efficiency and safety in its production facilities. By embracing the 5S principles and practices, XYZ Manufacturing achieved a 20% increase in productivity, a 30% reduction in accidents, and a significant improvement in employee morale and satisfaction.
Conclusion: Embrace the 5S Methodology for Workplace Excellence
In conclusion, the 5S Methodology offers organizations a powerful framework for achieving workplace excellence through organization, cleanliness, and standardization. By implementing the 5S principles and practices effectively and fostering a culture of continuous improvement, organizations can create a safer, more efficient, and more productive work environment for their employees.