In the realm of quality management, Poka-Yoke—also known as error-proofing—stands as a beacon of innovation and excellence. Originating from Japan, Poka-Yoke represents a proactive approach to quality control, where processes are designed to prevent errors from occurring rather than relying on detection and correction after the fact. Join us as we delve into the essence of Poka-Yoke, uncover best practices, and explore how to implement Poka-Yoke effectively in your organization.
Thank you for reading this post, don't forget to subscribe!Unveiling Poka-Yoke: The Art of Error-Proofing
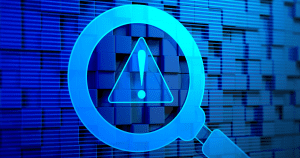
At its core, Poka-Yoke embodies the philosophy of “mistake-proofing,” where systems and processes are engineered to prevent errors before they occur. By incorporating design features, visual cues, and error-detection mechanisms, Poka-Yoke minimizes the risk of defects, enhances quality, and improves efficiency.
Key Principles of Poka-Yoke
1. Prevention over Detection
Poka-Yoke emphasizes the importance of preventing errors from occurring in the first place rather than relying on detection and correction after the fact. By designing processes and systems with built-in error-proofing features, organizations can minimize the risk of defects and improve overall quality.
2. Simplicity and Practicality
Central to Poka-Yoke is the principle of simplicity and practicality. Error-proofing solutions should be straightforward, easy to implement, and cost-effective, allowing organizations to achieve tangible improvements in quality without excessive complexity or investment.
3. Continuous Improvement
Poka-Yoke is a journey of continuous improvement, where organizations strive to identify and address potential sources of errors systematically. By soliciting input from frontline employees, monitoring process performance, and implementing corrective actions, organizations can refine their error-proofing solutions over time and drive ongoing quality improvements.
Implementing Poka-Yoke: Practical Strategies for Success
1. Identify Error-Prone Processes
Conduct a thorough analysis of your processes to identify potential sources of errors and defects. Focus on high-risk areas where errors are most likely to occur or have the greatest impact on quality, customer satisfaction, or safety.
2. Implement Error-Proofing Solutions
Develop and implement error-proofing solutions tailored to the specific needs and challenges of your organization. This may include redesigning workflows, incorporating visual cues, standardizing work procedures, or automating error-detection mechanisms.
3. Empower and Train Employees
Empower frontline employees to identify and address errors in real-time by providing training in Poka-Yoke principles and techniques. Encourage a culture of accountability, ownership, and continuous improvement, where employees actively contribute to error prevention efforts.
Real-World Impact of Poka-Yoke: A Case Study
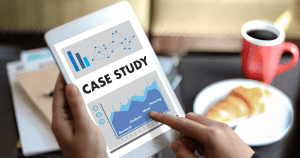
Let’s examine the success story of XYZ Corporation, a company that implemented Poka-Yoke to enhance quality and efficiency in its manufacturing process. By incorporating error-proofing features into its assembly line, XYZ Corporation achieved a 50% reduction in defects and a 30% increase in productivity within six months, resulting in significant cost savings and improved customer satisfaction.
Conclusion: Embrace Poka-Yoke for Quality Excellence
In conclusion, Poka-Yoke offers a powerful framework for achieving quality excellence by proactively preventing errors and defects in processes. By incorporating error-proofing solutions into workflows, empowering employees, and fostering a culture of continuous improvement, organizations can enhance quality, efficiency, and customer satisfaction.