Introduction – Mastering Just-in-Time (JIT) Production
In the realm of manufacturing excellence, Just-in-Time (JIT) Production stands as a testament to efficiency, productivity, and waste reduction. Originating from Japan, JIT is more than just a methodology; it’s a philosophy—a commitment to producing goods or services precisely when they are needed, in the exact quantity required, and with minimal waste. Join us as we explore the principles of JIT Production, uncover best practices, and learn how to implement JIT effectively in your organization.
Thank you for reading this post, don't forget to subscribe!Understanding Just-in-Time (JIT) Production: The Essence of Efficiency
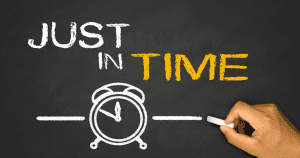
At its core, JIT Production revolves around the concept of eliminating waste and maximizing efficiency throughout the production process. By synchronizing production with customer demand, JIT minimizes inventory holding costs, reduces lead times, and enhances quality, responsiveness, and profitability.
Key Principles of JIT Production
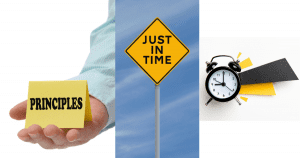
1. Demand-Driven Manufacturing
JIT Production operates on the principle of producing goods or services in response to customer demand. By aligning production with actual demand signals, organizations can avoid overproduction, reduce inventory costs, and minimize the risk of obsolete inventory.
2. Continuous Flow
JIT Production emphasizes the importance of maintaining a smooth and continuous flow of work throughout the production process. By minimizing interruptions, bottlenecks, and downtime, organizations can achieve higher throughput, shorter lead times, and greater flexibility to respond to changes in demand.
3. Pull System
Central to JIT Production is the pull system, where production is triggered by actual customer orders or consumption rather than forecasted demand. By pulling products through the production process based on real-time demand signals, organizations can avoid excess inventory buildup and reduce the risk of overproduction.
Implementing JIT Production: Practical Strategies for Success
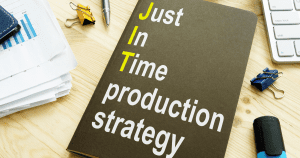
1. Streamline Production Processes
Identify and eliminate non-value-added activities, bottlenecks, and inefficiencies in your production processes. Implement lean manufacturing principles such as 5S, visual management, and standardized work to create a more streamlined and efficient workflow.
2. Foster Supplier Collaboration
Develop close relationships with suppliers and implement just-in-time inventory management practices to minimize lead times, reduce inventory holding costs, and improve supply chain efficiency. Collaborate with suppliers to establish Kanban systems, implement vendor-managed inventory (VMI) programs, and streamline order fulfillment processes.
3. Invest in Employee Training and Development
Empower employees with the skills, knowledge, and tools they need to contribute to the success of JIT Production. Provide training in lean manufacturing principles, problem-solving techniques, and quality improvement methodologies to foster a culture of continuous improvement and employee engagement.
Real-World Impact of JIT Production: A Case Study
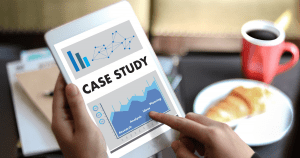
Let’s examine the success story of XYZ Manufacturing, a company that implemented JIT Production to transform its production process. By embracing JIT principles, XYZ Manufacturing achieved a 30% reduction in lead times, a 20% increase in productivity, and a significant improvement in on-time delivery performance, resulting in higher customer satisfaction and profitability.
Conclusion: Embrace JIT Production for Manufacturing Excellence
In conclusion, Just-in-Time (JIT) Production offers a powerful framework for achieving manufacturing excellence and operational efficiency. By embracing the principles of demand-driven manufacturing, continuous flow, and pull systems, organizations can streamline their production processes, reduce waste, and deliver value to customers with precision and speed.