Introduction: Mastering Jidoka
In the realm of manufacturing innovation, Jidoka—also known as autonomation—stands as a beacon of efficiency, quality, and empowerment. Rooted in the principles of lean manufacturing, Jidoka represents a harmonious blend of automation and human intelligence, where machines are equipped with the ability to detect abnormalities and stop production autonomously, empowering operators to intervene and resolve issues promptly. Join us as we delve into the essence of Jidoka, uncover best practices, and explore how to implement Jidoka effectively in your organization.
Thank you for reading this post, don't forget to subscribe!Understanding Jidoka: The Fusion of Automation and Intelligence
At its core, Jidoka embodies the philosophy of “automation with a human touch,” where machines are designed not only to perform tasks autonomously but also to detect and respond to abnormalities in the production process. By empowering machines to stop production when defects or abnormalities are detected, Jidoka enables operators to focus on value-added tasks and ensures that quality is built into the process from the outset.
Key Principles of Jidoka
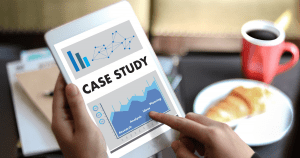
1. Autonomation
Jidoka involves equipping machines with sensors, detectors, and other automation technologies that enable them to monitor their own performance and detect abnormalities in real time. By autonomously stopping production when issues arise, machines prevent defective products from being produced and empower operators to address problems promptly.
2. Human Intelligence
Central to Jidoka is the recognition of the value of human intelligence and judgment in the manufacturing process. Operators play a critical role in monitoring production, interpreting data, and making informed decisions to resolve issues and improve processes. Jidoka enhances operator engagement and empowerment by enabling them to intervene in the production process when necessary.
3. Built-in Quality
Jidoka emphasizes the importance of building quality into the manufacturing process from the outset rather than inspecting for defects after production. By detecting and addressing abnormalities in real time, Jidoka helps prevent defects from being passed downstream, reducing rework, scrap, and customer complaints.
Implementing Jidoka: Practical Strategies for Success
1. Invest in Automation Technologies
Equip production equipment with sensors, detectors, and other automation technologies that enable them to detect abnormalities and stop production autonomously. Collaborate with technology vendors to integrate these features into existing machinery or invest in new equipment designed with Jidoka principles in mind.
2. Provide Operator Training and Support
Train operators to understand the principles of Jidoka, recognize abnormal conditions, and take appropriate action to address issues. Provide ongoing support and resources, such as visual aids, standard operating procedures, and troubleshooting guides, to empower operators to effectively utilize Jidoka in their daily work.
3. Foster a Culture of Continuous Improvement
Encourage operators to actively participate in problem-solving and process improvement initiatives. Implement feedback mechanisms, such as suggestion programs or quality circles, to solicit input from frontline workers and empower them to identify opportunities for optimization and innovation.
Real-World Impact of Jidoka: A Case Study
Let’s examine the success story of XYZ Manufacturing, a company that implemented Jidoka to enhance quality and productivity in its production process. By equipping its production equipment with Jidoka features and empowering operators to intervene when abnormalities were detected, XYZ Manufacturing achieved a 50% reduction in defects and a 30% increase in productivity within six months.
Conclusion: Embrace Jidoka for Manufacturing Excellence
In conclusion, Jidoka offers a powerful framework for achieving manufacturing excellence by combining automation with human intelligence. By empowering machines to detect abnormalities and empowering operators to intervene promptly, Jidoka enhances quality, productivity, and efficiency in the manufacturing process, driving continuous improvement and innovation.