Introduction: Andon System
In the realm of manufacturing excellence, the Andon System shines as a beacon of efficiency, empowerment, and continuous improvement. Originating from the Toyota Production System, the Andon System represents a visual management tool that enables frontline workers to identify, escalate, and resolve issues in real time, fostering a culture of transparency, collaboration, and problem-solving. Join us as we illuminate the essence of the Andon System, uncover industry best practices, and explore how to implement this powerful tool effectively in your manufacturing operations.
Thank you for reading this post, don't forget to subscribe!Shedding Light on the Andon System: A Tool for Real-Time Problem-Solving
The Andon System is more than just a signalling device; it’s a catalyst for driving operational excellence and quality improvement on the factory floor. By providing frontline workers with a visual means of communication, the Andon System enables rapid detection and response to production issues, minimizing downtime, reducing waste, and enhancing overall efficiency and productivity.
Key Components of the Andon System
Visual Signaling
At its core, the Andon System relies on visual signalling devices, such as lights or displays, to alert workers to production issues or abnormalities. These signals are often colour-coded to indicate the severity or type of problem, enabling quick identification and response by frontline teams.
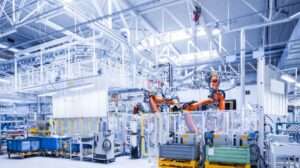
Escalation Process
The Andon System includes a predefined escalation process for addressing production issues, typically involving escalating the problem to a supervisor or support team for resolution. This process ensures that issues are addressed promptly and effectively, minimizing the impact on production schedules and quality standards.
Continuous Improvement
Central to the Andon System is the principle of continuous improvement, where frontline workers are empowered to identify and address root causes of production issues to prevent recurrence. By fostering a culture of problem-solving and collaboration, organizations can drive ongoing improvements in efficiency, quality, and safety.
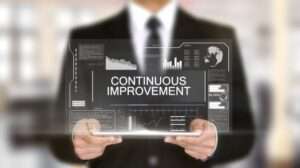
Implementing the Andon System: Practical Strategies for Success
Standardize Procedures
Develop standardized procedures for using the Andon System, including clear guidelines for when and how to activate the system, escalation protocols, and problem-solving methodologies. Provide training and support to ensure that all employees understand their roles and responsibilities.
Empower Frontline Workers
Empower frontline workers to use the Andon System to communicate production issues and propose solutions. Encourage a culture of ownership and accountability, where employees feel empowered to take initiative and drive continuous improvement in their work areas.
Monitor and Analyze Data
Regularly monitor and analyze data from the Andon System to identify trends, patterns, and areas for improvement. Use this information to implement targeted interventions, address systemic issues, and optimize production processes for greater efficiency and quality.
Real-World Impact of the Andon System: A Case Study
Let’s examine the success story of XYZ Manufacturing, a company that implemented the Andon System to enhance efficiency and quality on the factory floor. By empowering frontline workers to use the Andon System, XYZ Manufacturing achieved a 25% reduction in downtime, a 15% increase in productivity, and a significant improvement in product quality and customer satisfaction.
Conclusion: Illuminate Efficiency with the Andon System
In conclusion, the Andon System offers manufacturers a powerful tool for driving real-time problem-solving, efficiency, and quality improvement. By implementing the Andon System effectively and fostering a culture of collaboration and continuous improvement, organizations can unlock the full potential of their frontline teams and achieve excellence in manufacturing operations.