In the fast-paced landscape of modern business, Lean Management stands as a beacon of efficiency, innovation, and continuous improvement. Rooted in the principles of waste reduction and value creation, Lean Management offers organizations a systematic approach to streamlining processes, improving productivity, and delivering greater value to customers. Join us as we explore the essence of Lean Management, uncover industry best practices, and discover how to implement Lean principles effectively in your organization.
Thank you for reading this post, don't forget to subscribe!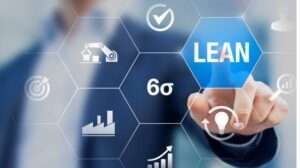
Unveiling Lean Management: The Art of Waste Reduction
Lean Management is more than just a methodology; it’s a mindset—a commitment to the relentless pursuit of efficiency and excellence. Originating from the Toyota Production System, Lean Management emphasizes the identification and elimination of waste in all forms, from excess inventory to unnecessary process steps, to drive greater value for customers and stakeholders.
Key Principles of Lean Management
Value Stream Mapping
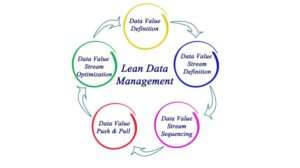
At the core of Lean Management is the concept of value stream mapping, which involves identifying all steps in a process and distinguishing between value-added and non-value-added activities. By eliminating waste and optimizing value-added processes, organizations can enhance efficiency and reduce costs.
Continuous Improvement
Lean Management promotes a culture of continuous improvement, where employees are empowered to identify opportunities for enhancement and implement incremental changes to achieve greater efficiency and effectiveness. Through initiatives such as Kaizen events and daily improvement activities, organizations can drive ongoing progress and innovation.
Respect for People
Central to Lean Management is the principle of respect for people, which emphasizes the importance of empowering employees, fostering collaboration, and creating a supportive work environment. By valuing and engaging frontline workers, organizations can unlock their full potential and drive sustainable improvement.
Implementing Lean Management: Practical Strategies for Success
Identify and Prioritize Improvement Opportunities
Begin by conducting a thorough assessment of your organization’s processes to identify areas of waste and inefficiency. Prioritize improvement opportunities based on their potential impact on customer satisfaction, cost reduction, and operational efficiency.
Engage and Empower Employees
Empower employees at all levels of the organization to participate in Lean initiatives and contribute their insights and ideas for improvement. Provide training and support to help employees understand Lean principles and methodologies and encourage a culture of collaboration and continuous learning.
Measure and Monitor Progress
Establish key performance indicators (KPIs) to measure the effectiveness of Lean initiatives and track progress over time. Regularly review performance metrics, celebrate successes, and identify areas for further improvement to sustain momentum and drive ongoing progress.
Real-World Impact of Lean Management: A Case Study
Let’s examine the success story of XYZ Corporation, a company that embraced Lean Management to transform its operations and achieve significant improvements in efficiency and profitability. By implementing Lean principles and practices, XYZ Corporation achieved a 30% reduction in lead times, a 20% increase in productivity, and a substantial improvement in customer satisfaction.
Conclusion: Embrace Lean Management for Operational Excellence
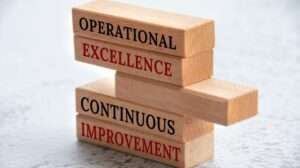
In conclusion, Lean Management offers organizations a powerful framework for driving operational excellence through waste reduction, continuous improvement, and respect for people. By adopting Lean principles and practices, organizations can streamline processes, enhance productivity, and deliver greater value to customers, positioning themselves for long-term success and competitiveness in today’s dynamic business environment.